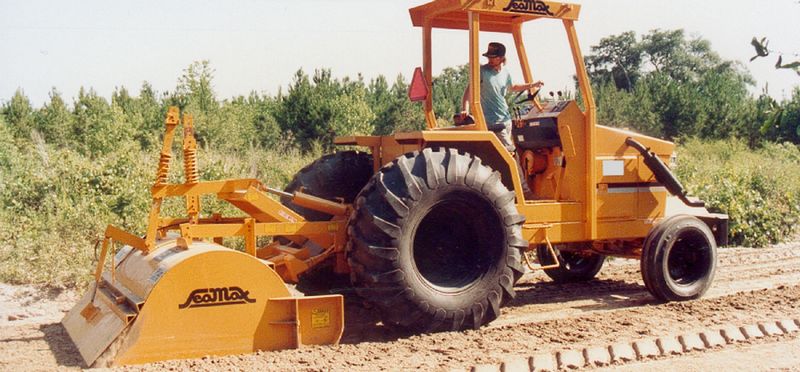
Essential Equipment for Ensuring Stability: An Overview of Stabilization Equipment
Stabilization equipment plays a crucial role in various industries, helping to ensure stability and safety in different applications. From construction sites to film sets, stabilization equipment is used to prevent accidents and maintain balance in challenging environments.
Stabilization equipment includes a wide range of tools and devices that are designed to stabilize and support structures, equipment, and objects. These tools are often used in situations where there is a risk of instability or imbalance, such as during construction, transportation, or heavy lifting operations.
One example of stabilization equipment is a jack, which is commonly used to lift and stabilize heavy objects. Jacks come in various types, including hydraulic jacks, bottle jacks, and scissor jacks, each designed for specific applications. Another example is a leveling system, which is used to ensure that a structure or object is perfectly level. These systems often use lasers or bubble levels to provide accurate measurements.
Stabilization equipment is also essential in the film industry, where camera stabilization devices, such as gimbals and tripods, are used to capture smooth and steady shots. These devices help eliminate camera shakes and vibrations, resulting in professional-looking footage.
Overall, stabilization equipment plays a vital role in ensuring stability and safety in various industries. Whether it’s lifting heavy objects, leveling structures, or capturing stable footage, these tools and devices help maintain balance and prevent accidents in challenging environments.
What equipment is used for soil stabilization?
Soil stabilization is the process of improving the physical properties of soil to increase its strength and durability. Various types of equipment are used to achieve effective soil stabilization. Here are some commonly used equipment:
-
Soil Stabilizer/Reclaimer: This machine is used to mix and blend soil with stabilizing agents, such as lime, cement, or asphalt. It helps in homogenizing the soil and distributing the stabilizing agents evenly.
-
Grader: A grader is used to level the soil surface and provide a smooth and even grade. It helps in removing any irregularities, such as bumps or depressions, which can affect the stability of the soil.
-
Roller Compactor: A roller compactor is used to compact the soil after stabilization. It applies pressure on the soil surface, reducing air voids and increasing soil density. This improves the load-bearing capacity of the soil and prevents settlement.
-
Paver: A paver is used to lay a stabilizing layer, such as asphalt or concrete, on the soil surface. It helps in creating a stable and durable surface, suitable for heavy traffic loads.
-
Water Truck: A water truck is used to moisten the soil before stabilization. It helps in achieving optimal moisture content, which is essential for proper mixing and compaction of the soil.
-
Testing Equipment: Various testing equipment, such as soil compaction testers, moisture content meters, and strength testing devices, are used to assess the effectiveness of soil stabilization and ensure the desired quality of the stabilized soil.
These are some of the equipment commonly used for soil stabilization. The selection of equipment depends on factors such as the type of soil, the desired level of stabilization, and the specific requirements of the project.
Overview of equipment for different methods
When it comes to stabilization, there are several methods that can be used depending on the situation and requirements. Each method requires specific equipment to achieve the desired results.
1. Mechanical stabilization:
For mechanical stabilization, equipment such as excavators, bulldozers, and graders are used. These machines are used to move and compact soil, creating a stable surface for construction or other activities.
2. Chemical stabilization:
Chemical stabilization involves the use of additives to improve the properties of soil. Equipment such as spreaders, mixers, and sprayers are used to apply the additives evenly and effectively. These machines ensure that the additives are distributed uniformly throughout the soil.
3. Geosynthetic stabilization:
Geosynthetics, such as geotextiles and geogrids, are used in geosynthetic stabilization. Equipment such as rollers and compactors are used to install and compact these materials. These machines ensure that the geosynthetics are properly integrated into the soil, providing reinforcement and stabilization.
4. Structural stabilization:
Structural stabilization involves the use of physical structures to provide stability. Equipment such as pile drivers, concrete mixers, and cranes are used to construct these structures. These machines are essential for building structures such as retaining walls, foundations, and embankments.
Overall, the choice of equipment depends on the specific stabilization method being used. It is important to select the right equipment and use it correctly to ensure effective stabilization and long-term stability.
Primary and auxiliary equipment
Primary equipment:
The primary equipment used in stabilization systems includes:
- Stabilizer bars: These are used to reduce body roll and improve stability during cornering. They connect the left and right sides of the suspension system.
- Shock absorbers: These dampen the movement of the springs and help maintain the stability of the vehicle. They absorb the energy generated by bumps and uneven road surfaces.
- Springs: These provide support and help absorb the impact of road irregularities. They help keep the vehicle level and stable.
- Control arms: These connect the suspension system to the vehicle’s frame or body. They help control the movement of the wheels and provide stability.
- Anti-lock braking system (ABS): This system helps prevent the wheels from locking up during braking, improving stability and control.
Auxiliary equipment:
In addition to the primary equipment, stabilization systems may also include auxiliary equipment, such as:
- Electronic stability control (ESC): This system helps maintain stability and control by automatically applying individual brakes and reducing engine power when necessary.
- Traction control system (TCS): This system helps prevent wheel spin and loss of traction by applying brakes to the spinning wheels or reducing engine power.
- Roll stability control (RSC): This system helps prevent rollovers by applying brakes to individual wheels and reducing engine power to counteract the forces that can cause a vehicle to roll over.
- Active suspension system: This system adjusts the suspension settings in real-time to provide optimal stability and comfort.
- Steering assist: This system provides additional assistance to the driver when steering, improving stability and control.
These primary and auxiliary equipment components work together to improve the stability, control, and safety of vehicles equipped with stabilization systems.
Equipment requirements
When it comes to stabilizing equipment, there are several requirements that need to be considered. These requirements ensure that the equipment is capable of effectively stabilizing various structures and environments.
1. Load capacity: The equipment must have a sufficient load capacity to support the weight of the structure or object it is being used to stabilize. This includes considering factors such as the weight distribution and any additional loads that may be applied during stabilization.
2. Adjustability: The equipment should be adjustable to accommodate different sizes and configurations of structures. This allows for flexibility in its application and ensures that it can be used in various scenarios.
3. Durability: Stabilization equipment needs to be durable and able to withstand the rigors of the stabilization process. It should be made from high-quality materials that can resist corrosion, wear, and tear, ensuring its longevity and reliability.
4. Portability: In many cases, stabilization equipment needs to be portable to facilitate its transportation and use in different locations. Portability allows for ease of deployment and ensures that the equipment can be readily available when needed.
5. Safety features: Safety is paramount when using stabilizing equipment. It should be equipped with safety features such as non-slip surfaces, secure locking mechanisms, and clear instructions for use. These features help to minimize the risk of accidents and ensure the well-being of the operators and surrounding personnel.
6. Compatibility: The equipment should be compatible with other stabilization systems and tools. This allows for integration with existing systems and enhances the overall effectiveness of the stabilization process.
7. Ease of use: Stabilization equipment should be user-friendly and easy to operate. Clear instructions and intuitive controls make it easier for operators to use the equipment effectively and efficiently.
8. Maintenance requirements: Regular maintenance is necessary to ensure the equipment remains in optimal working condition. The equipment should have clear maintenance requirements, including routine inspections, cleaning procedures, and guidelines for replacing worn or damaged parts.
By considering these equipment requirements, you can ensure that the stabilizing equipment you choose is capable of effectively stabilizing structures and environments, providing safety and peace of mind.
What machines are used for mixing soil with stabilizing additives?
When it comes to mixing soil with stabilizing additives, there are several machines that can be used for this purpose. These machines are specifically designed to ensure thorough and efficient mixing, resulting in a stabilized soil that is suitable for construction projects. The following are some common machines used for this process:
1. Pugmill Mixers: Pugmill mixers are commonly used for mixing soil with stabilizing additives. These machines consist of a mixing chamber and a conveyor belt system. The soil and stabilizing additives are fed into the mixing chamber, where they are thoroughly mixed. The conveyor belt then transports the mixture to the desired location.
2. Cement Stabilizers: Cement stabilizers are machines that are specifically designed for mixing soil with cement as a stabilizing additive. These machines typically have a rotating drum or blades that mix the soil and cement together. They are commonly used in road construction projects.
3. Lime Stabilizers: Lime stabilizers are similar to cement stabilizers, but they are used for mixing soil with lime as a stabilizing additive. These machines also have a rotating drum or blades for thorough mixing. Lime stabilizers are commonly used in soil stabilization for foundations and other construction projects.
4. Mixing Attachments: Some construction equipment, such as excavators and skid steer loaders, can be equipped with mixing attachments for soil stabilization. These attachments are designed to mix soil with stabilizing additives efficiently. They can be easily attached to the equipment and provide versatility in mixing soil in various locations.
5. Stabilization Plants: Stabilization plants are larger machines that are used for large-scale soil stabilization projects. These plants typically have multiple mixing chambers and conveyor systems to handle large quantities of soil and stabilizing additives. They are often used in major construction projects such as highways and airports.
Overall, these machines play a crucial role in the process of mixing soil with stabilizing additives. They ensure that the additives are thoroughly mixed with the soil, resulting in a stable and durable construction material.
Types of mixing machines
1. Batch mixers: These mixing machines are commonly used in small-scale operations where a specific amount of materials needs to be mixed at a time. Batch mixers are versatile and can handle a wide range of materials, including powders, liquids, and pastes. They typically consist of a mixing chamber, agitator, and a motor that rotates the agitator to mix the materials.
2. Continuous mixers: As the name suggests, continuous mixers are designed to mix materials continuously, making them suitable for large-scale operations. These machines are typically used in industries such as food processing, chemical manufacturing, and pharmaceuticals. Continuous mixers can process a high volume of materials and provide a consistent and uniform mixture.
3. Planetary mixers: Planetary mixers are versatile machines that are commonly used in the baking industry. They have a unique mixing action that involves a revolving blade, which rotates around the mixing bowl while the agitator spins on its own axis. This dual rotation ensures thorough mixing and kneading of dough and other ingredients.
4. Ribbon mixers: Ribbon mixers are commonly used in industries that require gentle mixing of powders, granules, and other dry materials. These machines have a horizontal, U-shaped trough with a ribbon-like agitator that rotates at a low speed. The ribbon agitator moves the materials in a spiral motion, ensuring a consistent and homogeneous mixture.
5. High-shear mixers: High-shear mixers are designed to handle materials that are difficult to mix, such as viscous liquids, pastes, and gels. These machines use a rotor-stator system, where a high-speed rotor generates a strong shear force that breaks down particles and promotes mixing. High-shear mixers are commonly used in industries such as cosmetics, pharmaceuticals, and chemicals.
6. Paddle mixers: Paddle mixers are simple and cost-effective mixing machines that are commonly used in industries such as construction, agriculture, and animal feed production. These machines have a horizontal drum or trough with paddles that rotate on a central shaft. The paddles lift and tumble the materials, ensuring a thorough and even mixture.
7. Vacuum mixers: Vacuum mixers are used in industries that require mixing under reduced pressure, such as the pharmaceutical and food industries. These machines create a vacuum environment inside the mixing chamber, which helps remove air bubbles and prevent oxidation. Vacuum mixers are commonly used for mixing sensitive materials that can be affected by exposure to air.
8. Homogenizers: Homogenizers are specialized mixing machines that are used to create emulsions, suspensions, and dispersions. These machines use high pressure and shear forces to break down particles and create a uniform mixture. Homogenizers are commonly used in industries such as food and beverage, pharmaceuticals, and cosmetics.
Each type of mixing machine has its own advantages and applications, and the choice of machine depends on the specific requirements of the process and the materials being mixed.
Criteria for choosing specific models
When selecting stabilization equipment, it is important to consider several criteria that will help you choose the most suitable model for your needs. These criteria include:
Criteria | Description |
---|---|
Load Capacity | The maximum weight that the equipment can handle. It is important to choose a model that can support the weight of your equipment to ensure stability and safety. |
Size and Weight | The dimensions and weight of the equipment should be suitable for your intended use. Consider the portability and ease of transportation when selecting a model. |
Adjustability | Some models offer adjustable features such as height, tilt, or pan. These adjustable features can greatly enhance the flexibility and versatility of the equipment. |
Compatibility | Ensure that the stabilization equipment is compatible with your camera or other equipment. Check the mounting options and specifications to ensure a proper fit. |
Build Quality | Consider the durability and construction of the equipment. Look for models made from high-quality materials that can withstand regular use and provide long-lasting performance. |
Price | Set a budget for your equipment and compare prices to find a model that offers the best value for your money. Remember to consider the features and quality in relation to the price. |
By considering these criteria, you can make an informed decision and choose a specific model of stabilization equipment that best fits your requirements and preferences.
Features of working with different additives
When using stabilization equipment, it is important to consider the different additives that can be used. These additives can enhance the performance and effectiveness of the equipment. Here are some features to consider when working with different additives:
- Chemical composition: Different additives have different chemical compositions, which can affect their compatibility with the stabilization equipment. It is important to understand the chemical composition of the additives and ensure that they are compatible with the equipment being used.
- Dosage: The dosage of the additives can vary depending on the desired effect and the specific equipment being used. It is important to follow the recommended dosage guidelines provided by the manufacturer to ensure optimal performance.
- Compatibility: Some additives may not be compatible with certain types of stabilization equipment. It is important to check the compatibility of the additives with the equipment before use to avoid any adverse reactions or damage.
- Effectiveness: Different additives may have different levels of effectiveness in stabilizing equipment. It is important to choose additives that are proven to be effective and have a track record of success in similar applications.
- Storage and handling: Some additives may require specific storage and handling conditions to maintain their effectiveness. It is important to carefully follow the storage and handling instructions provided by the manufacturer to ensure the additives remain in optimal condition.
- Environmental impact: It is important to consider the environmental impact of different additives. Some additives may have a negative impact on the environment, while others may be more environmentally friendly. It is important to choose additives that align with environmental regulations and guidelines.
By considering these features when working with different additives, it is possible to enhance the performance and effectiveness of stabilization equipment.
How is the quality of soil stabilization controlled?
Controlling the quality of soil stabilization is essential to ensure that the desired outcomes are achieved and that the stabilized soil meets the necessary requirements. There are several methods and techniques that are commonly used to control the quality of soil stabilization:
1. Laboratory Testing: Laboratory testing is conducted to analyze the properties of the soil and determine its suitability for stabilization. Various tests, such as the Atterberg limits test, compaction test, and California bearing ratio test, are performed to assess the soil’s strength, plasticity, and compactability.
2. Field Testing: Field testing involves conducting tests on the stabilized soil at the construction site. This helps to ensure that the stabilization process is carried out correctly and that the desired results are achieved. Field tests, such as the plate load test and dynamic cone penetration test, are performed to assess the strength and compaction of the stabilized soil.
3. Quality Control Monitoring: Quality control monitoring involves regular inspections and measurements during the soil stabilization process. This helps to identify any issues or deviations from the desired specifications and allows for timely corrective actions. Quality control monitoring may include checking the mixing ratios, moisture content, and compaction levels of the stabilized soil.
4. Documentation: Proper documentation is crucial for controlling the quality of soil stabilization. Detailed records of laboratory test results, field test results, and quality control monitoring observations should be maintained. This documentation provides a reference for future analysis and helps in identifying any trends or patterns that may affect the quality of soil stabilization.
5. Training and Certification: Ensuring that personnel involved in soil stabilization are properly trained and certified is another important aspect of quality control. Training programs should cover the proper techniques and procedures for soil stabilization, as well as the importance of quality control measures. Certification programs can help establish a standard level of competency and ensure that personnel are knowledgeable and skilled in performing soil stabilization activities.
By implementing these quality control measures, the quality of soil stabilization can be effectively controlled and maintained. This helps to ensure the stability and durability of the stabilized soil, thereby enhancing the overall success of the construction project.
Control methods at different stages
Stabilization equipment is crucial for controlling and maintaining stability in various industries, such as construction, mining, and oil and gas. Different control methods are employed at different stages of the stabilization process to ensure optimal performance and safety.
During the initial stage of stabilization, preliminary assessments are conducted to determine the specific requirements and potential risks. This involves evaluating the terrain, soil conditions, and other factors that may affect stability. Control methods at this stage include geotechnical surveys, site investigations, and data analysis to identify potential challenges and develop appropriate stabilization strategies.
Once the initial assessments are completed, design and planning become essential. Control methods during this stage involve the selection of suitable stabilization equipment based on the project’s requirements. This may include the use of ground improvement techniques, such as soil mixing, deep soil mixing, or jet grouting, to enhance the soil’s mechanical properties and increase stability.
During the construction phase, control methods focus on monitoring and ensuring the proper implementation of stabilization measures. This involves regular inspections, quality control checks, and adherence to design specifications. Advanced technologies, such as automated monitoring systems and real-time data analysis, are employed to detect any deviations or potential issues that may arise during construction.
After the stabilization measures are implemented, ongoing monitoring and maintenance are crucial to ensure long-term stability. Control methods at this stage involve periodic inspections, performance assessments, and maintenance activities. This allows for early identification of any deterioration or changes in stability conditions, enabling timely corrective measures to be taken.
In summary, control methods at different stages of the stabilization process play a vital role in achieving and maintaining stability. By employing appropriate control methods, industries can ensure the safety and performance of their stabilization equipment, contributing to the success of their projects.
Responsibility for quality control
Ensuring the quality of stabilization equipment is crucial for its safe and effective use. The responsibility for quality control lies with the manufacturer, as well as the regulatory authorities and end-users.
Manufacturers are responsible for designing and producing stabilization equipment that meets the required standards and specifications. They must implement quality control measures throughout the manufacturing process to ensure the reliability and performance of their products. This includes conducting rigorous testing and inspections, as well as adhering to industry regulations and guidelines.
Regulatory authorities play a vital role in overseeing the quality of stabilization equipment. They establish and enforce regulations and standards that manufacturers must comply with. Regulatory bodies also conduct inspections and audits to verify compliance and ensure that the equipment meets the necessary safety requirements. They may issue certifications and licenses to manufacturers that demonstrate a commitment to quality control.
End-users have a responsibility to perform regular inspections and maintenance on the stabilization equipment they use. This includes checking for any signs of wear or damage, as well as ensuring that all components are functioning correctly. End-users should also follow the manufacturer’s instructions for proper use and storage of the equipment.
In conclusion, responsibility for quality control of stabilization equipment lies with the manufacturers, regulatory authorities, and end-users. By working together, they can ensure that the equipment is safe, reliable, and performs its intended function.
Quality assessment criteria
When evaluating stabilization equipment, there are several quality assessment criteria that should be considered. These criteria help determine the overall performance and reliability of the equipment, ensuring that it meets the necessary standards and requirements. The following are some key criteria to consider:
- Durability: The equipment should be built to withstand heavy usage and harsh environmental conditions. It should be made from high-quality materials that are resistant to corrosion, wear, and tear.
- Accuracy: The equipment should provide accurate and consistent stabilization. This is crucial for achieving precise stabilization results and ensuring the safety of the equipment user.
- Stability: The equipment should be stable and secure during operation. It should not wobble or move excessively, as this can lead to inaccurate stabilization and potential accidents.
- Ease of use: The equipment should be user-friendly and easy to operate. It should have clear instructions and intuitive controls, allowing users to quickly and efficiently stabilize their equipment.
- Maintenance: The equipment should be easy to maintain and service. It should have accessible components that can be easily replaced or repaired, minimizing downtime and ensuring continuous operation.
- Safety: The equipment should meet all safety standards and regulations. It should have safety features such as emergency stop buttons, overload protection, and safety guards to prevent accidents and injuries.
By considering these quality assessment criteria, you can ensure that the stabilization equipment you choose is reliable, efficient, and safe to use. It is essential to carefully evaluate these criteria when selecting equipment for your specific stabilization needs.
What equipment is needed for applying different types of stabilizing substances?
When it comes to applying different types of stabilizing substances, there are several essential pieces of equipment that are commonly used. These include:
1. Sprayers: Sprayers are a fundamental tool for applying stabilizing substances. They are available in various sizes and types, such as handheld sprayers, backpack sprayers, and motorized sprayers. The choice of sprayer depends on the size of the area to be treated and the type of stabilizer being used.
2. Mixing containers: Mixing containers are necessary for preparing the stabilizing substances. These containers should be clean, sturdy, and large enough to hold the required amount of stabilizer and any other additives.
3. Stirring equipment: Stirring equipment, such as a paddle mixer or a stirring rod, is used to mix the stabilizing substance thoroughly. This ensures that all the components are evenly distributed and the stabilizer is ready for application.
4. Safety equipment: Safety should always be a priority when working with stabilizing substances. Personal protective equipment (PPE), including gloves, goggles, and masks, should be worn to protect against any potential hazards.
5. Application tools: Depending on the type of stabilizer and the intended surface, different application tools may be required. These can include brushes, rollers, or squeegees. The choice of application tool will depend on factors such as the thickness of the stabilizer and the desired finish.
6. Measuring equipment: Accurate measurement of stabilizing substances is crucial for achieving the desired results. Measuring equipment, such as measuring cups or scales, should be used to ensure the correct ratio of stabilizer to other additives.
7. Cleaning equipment: After the application is complete, it is important to clean all equipment thoroughly. This includes rinsing sprayers, cleaning mixing containers, and washing application tools. Proper cleaning ensures that the equipment is ready for future use and prevents any cross-contamination.
Overall, having the right equipment is essential for the successful application of different types of stabilizing substances. It not only ensures efficient and accurate application but also promotes safety and longevity of the equipment.
Equipment for each type of substance
When it comes to stabilizing different types of substances, there is a wide range of equipment available. The choice of equipment depends on the specific characteristics and properties of the substance being stabilized. Here are some examples:
Liquids:
For stabilizing liquids, one common piece of equipment is a stabilization tank. This tank is designed to hold the liquid and prevent it from sloshing around during transportation or storage. It typically has baffles or other internal structures to minimize movement and ensure stability.
Gases:
When it comes to stabilizing gases, one key piece of equipment is a pressure regulator. This device helps to control the pressure of the gas, ensuring that it remains stable and within safe limits. Pressure regulators can be manual or automatic, and they come in various sizes and designs to accommodate different types of gases.
Solids:
Stabilizing solids often involves the use of containers or bins with specialized features. For example, a hopper or silo may be used to store and stabilize bulk solids. These containers are designed to prevent the solids from shifting or settling, ensuring their stability during transportation or processing.
Chemicals:
When it comes to stabilizing chemicals, specialized equipment such as chemical stabilizers or inhibitors may be used. These substances are added to the chemical to prevent degradation or reactions that could lead to instability. Chemical stabilizers can be added directly to the chemical or incorporated into the packaging materials to ensure long-term stability.
Biological substances:
Stabilizing biological substances, such as vaccines or biological samples, often requires specialized equipment like cryogenic storage systems. These systems use extremely low temperatures to preserve the biological material and prevent degradation. Cryogenic storage systems typically include cryo-tanks or freezers that maintain the required temperature for long-term stability.
Overall, the choice of equipment for stabilizing different substances depends on their specific characteristics and requirements. Proper selection and use of the right equipment are crucial to ensure the stability and integrity of the substances.
Key criteria for choosing equipment
When it comes to selecting stabilization equipment, there are several important criteria to consider. These factors can help ensure that the chosen equipment is suitable for the specific application and provides the desired level of stability.
1. Load capacity: It is crucial to determine the maximum load capacity required for the equipment. This will depend on the weight of the objects or structures that need to be stabilized. Choosing equipment with a higher load capacity than necessary can lead to unnecessary expenses, while selecting equipment with a lower load capacity can compromise safety.
2. Adjustability: The ability to adjust the equipment to different heights, angles, or positions is essential. This ensures versatility and adaptability to various stabilization requirements. Adjustable equipment allows for precise positioning, enhancing stability and safety.
3. Durability: Stabilization equipment should be made of high-quality materials that can withstand the demands of the application. It should be resistant to corrosion, wear, and tear, ensuring a long service life. This is especially important for equipment used in harsh environments or heavy-duty applications.
4. Portability: Depending on the specific needs, portability may be a crucial factor. Equipment that is lightweight, compact, and easy to transport can be advantageous, especially for fieldwork or situations where mobility is necessary.
5. Safety features: Safety should be a top priority when choosing stabilization equipment. Look for features such as non-slip surfaces, secure locking mechanisms, and built-in safety measures. These features help prevent accidents and ensure the well-being of the operators and the stability of the objects or structures being stabilized.
6. Cost-effectiveness: While cost is an important aspect, it should not be the sole determining factor. Consider the overall value that the equipment provides, including its quality, durability, and performance. Investing in high-quality equipment may be more cost-effective in the long run, as it can reduce maintenance and replacement costs.
By carefully considering these key criteria, individuals and organizations can make informed decisions when selecting stabilization equipment. Taking into account the specific requirements and constraints of the application will lead to optimal choices that meet the desired level of stability and performance.
Specifics of equipment for different objects
Stabilization equipment plays a crucial role in ensuring the safety and stability of various objects, such as buildings, bridges, and offshore structures. The specific requirements for equipment may vary depending on the type and purpose of the object. In this section, we will discuss the specifics of equipment for different objects.
Buildings
When it comes to stabilizing buildings, the equipment used must be able to withstand the weight and forces exerted by the structure. This often includes the use of hydraulic jacks, steel braces, and tensioning systems. The equipment must be able to provide support and distribute the load evenly to prevent any structural damage or collapse.
Bridges
For bridges, the equipment used for stabilization must be able to handle not only the weight of the structure but also the dynamic loads caused by traffic and environmental factors. This often involves the use of specialized hydraulic jacks, steel cables, and dampers. The equipment must be able to absorb and dissipate the energy generated by these dynamic forces to ensure the stability and integrity of the bridge.
Offshore structures
Offshore structures, such as oil rigs and platforms, face unique challenges due to their exposure to harsh marine conditions. The equipment used for stabilization must be able to withstand corrosive environments, high winds, and large waves. This often includes the use of heavy-duty hydraulic systems, mooring systems, and dynamic positioning systems. The equipment must be able to provide a stable base and compensate for the movement caused by waves and currents.
Object Type | Specific Equipment |
---|---|
Buildings | Hydraulic jacks, steel braces, tensioning systems |
Bridges | Specialized hydraulic jacks, steel cables, dampers |
Offshore structures | Heavy-duty hydraulic systems, mooring systems, dynamic positioning systems |
In conclusion, the specifics of equipment for different objects depend on their type and purpose. Whether it is a building, a bridge, or an offshore structure, the equipment used must be tailored to meet the unique requirements and challenges of each object.
What requirements are imposed on equipment for soil stabilization?
Equipment for soil stabilization plays a crucial role in achieving effective and efficient stabilization results. It is important for the equipment to meet certain requirements to ensure successful soil stabilization projects. The following are some key requirements imposed on equipment for soil stabilization:
- Reliability: The equipment should be reliable and capable of handling the demands of soil stabilization processes. It should be able to withstand harsh conditions and continue functioning without breakdowns.
- Flexibility: The equipment should be flexible and adaptable to different soil types and conditions. It should be able to handle varying soil properties and adjust accordingly to achieve optimal stabilization results.
- Accuracy: Precision is crucial in soil stabilization. The equipment should be accurate in measuring and applying stabilization agents, such as cement or lime, to ensure the desired stabilization levels are achieved.
- Efficiency: Efficient equipment is essential to complete soil stabilization projects within the allocated timeframes. It should be able to perform the necessary tasks in a timely manner, ensuring productivity and cost-effectiveness.
- Safety: Equipment used in soil stabilization should prioritize safety. It should have safety features and mechanisms in place to minimize the risk of accidents or injuries to workers operating the equipment.
- Maintainability: The equipment should be easy to maintain and repair. Regular maintenance and timely repairs are necessary to ensure the equipment remains in optimal working condition, minimizing downtime during soil stabilization projects.
- Environmental considerations: Equipment used in soil stabilization should adhere to environmental regulations and minimize any negative impact on the environment. It should be designed to minimize emissions and prevent soil and water contamination.
By meeting these requirements, equipment for soil stabilization can effectively contribute to the success of soil stabilization projects, ensuring stable and durable soil structures.
Basic requirements for technical characteristics
When it comes to stabilization equipment, there are certain basic requirements for its technical characteristics that need to be met. These requirements ensure that the equipment is capable of performing its intended function effectively and efficiently. Some of the key technical characteristics that should be considered are:
Characteristic | Description |
---|---|
Stability | The equipment should have a stable base or foundation to prevent any unnecessary movement or shaking during operation. This is crucial for maintaining the stability of the equipment and ensuring accurate results. |
Precision | The equipment should be capable of providing precise measurements or adjustments. This is especially important in applications where even slight deviations can have significant impacts. |
Versatility | The equipment should be versatile enough to be used in various applications or environments. It should be able to adapt to different conditions and requirements without compromising its performance. |
Durability | The equipment should be durable and able to withstand harsh conditions or heavy usage. It should be constructed using high-quality materials that can resist wear, corrosion, and other forms of damage. |
Ease of use | The equipment should be user-friendly and easy to operate. It should have clear instructions and intuitive controls to minimize the learning curve and maximize efficiency. |
Safety | The equipment should meet all relevant safety standards and regulations. It should have safety features in place to protect the user and prevent any accidents or injuries. |
By considering these basic requirements for the technical characteristics of stabilization equipment, users can ensure that they are investing in reliable and high-performing equipment that meets their specific needs and requirements.
Safety and reliability requirements
Safety and reliability are crucial factors when it comes to stabilization equipment. The nature of the equipment and the conditions it operates in demand strict adherence to safety regulations and the highest level of reliability.
One of the primary safety requirements is to ensure the equipment is designed and manufactured to withstand the expected loads and stresses. This includes conducting thorough analysis and testing to ensure the equipment’s structural integrity. Additionally, safety features such as emergency stop buttons and protective guards should be incorporated into the design to prevent accidents and injuries.
Reliability requirements involve ensuring that the equipment performs its intended function consistently and without failure. This includes using high-quality materials and components that can withstand the harsh operating conditions. Regular maintenance and inspections are also necessary to identify and address any potential issues before they develop into major problems.
In addition to the equipment itself, safety and reliability requirements extend to the personnel operating and maintaining the equipment. Adequate training should be provided to ensure they have the necessary knowledge and skills to operate the equipment safely. Regular safety drills and refresher courses should also be conducted to keep the operators up to date with the latest safety protocols.
Overall, safety and reliability requirements are essential to ensure the effective and safe operation of stabilization equipment. By meeting these requirements, companies can minimize the risk of accidents, protect personnel, and maintain the integrity of their operations.
Operational requirements
1. Stability: Stabilization equipment must provide a stable platform for various operations. It should be able to minimize the effects of vibrations, movements, and external factors that may affect the performance of the equipment.
2. Durability: The equipment should be able to withstand harsh environmental conditions, such as extreme temperatures, humidity, and vibrations. It should be made of high-quality materials that can resist corrosion and wear and tear.
3. Precision: The equipment should have precise controls and mechanisms to ensure accurate stabilization. It should be able to maintain stability within a specified range, even during dynamic movements or changes in the environment.
4. Flexibility: Stabilization equipment should be adaptable to different operating conditions and requirements. It should be able to support various payloads and be easily adjustable to accommodate specific needs.
5. Power efficiency: The equipment should be designed to consume minimal power while providing optimal stabilization performance. It should be energy-efficient and have low power requirements to prolong battery life and reduce operational costs.
6. User-friendly interface: The equipment should have a user-friendly interface that allows operators to easily control and adjust stabilization settings. It should provide clear feedback and indicators to ensure smooth operation and efficient troubleshooting.
7. Safety: Stabilization equipment should prioritize the safety of operators and surrounding personnel. It should have built-in safety features, such as overload protection and emergency stop functions, to prevent accidents and injuries.
8. Maintenance and support: The equipment should be easy to maintain and service. It should have accessible components for troubleshooting and repair, and there should be readily available technical support and spare parts for efficient maintenance.
9. Compatibility: Stabilization equipment should be compatible with other relevant systems and technologies, such as cameras, sensors, and communication devices. It should have the necessary interfaces and protocols to integrate seamlessly with other equipment.
10. Reliability: The equipment should be reliable and able to perform consistently in various operating conditions. It should have a low failure rate and be able to withstand long hours of continuous operation without compromising performance.
How to properly select equipment for soil stabilization at a facility?
Soil stabilization is an important process in construction and engineering projects. It involves improving the properties of soil to increase its load-bearing capacity and reduce settlement. To achieve effective soil stabilization, it is crucial to select the right equipment for the job. Here are some factors to consider when choosing equipment for soil stabilization at a facility:
- Soil type: Different soils require different stabilization techniques and equipment. Consider the type of soil at your facility and choose equipment that is suitable for that soil type. For example, cohesive soils may require deep soil mixing equipment, while granular soils may benefit from the use of vibratory compactors.
- Project requirements: Assess the specific requirements of your project. Determine the desired level of soil stabilization, the area to be treated, and the available time frame. This information will help you select equipment that is capable of meeting these requirements efficiently.
- Equipment capabilities: Evaluate the capabilities of different stabilization equipment. Consider factors such as the depth and width of treatment, the speed of operation, and the power source required. Choose equipment that is capable of delivering the desired results within the project constraints.
- Availability: Check the availability of the equipment in your area. Some specialized equipment may not be readily available, which could cause delays in the project. Ensure that the chosen equipment is accessible and can be delivered in a timely manner.
- Cost: Consider the cost of the equipment and its operational expenses. Compare prices from different suppliers and weigh them against the benefits offered by the equipment. Keep in mind that quality and reliability should not be compromised for cost savings.
Properly selecting equipment for soil stabilization is crucial for the success of any facility project. By considering factors such as soil type, project requirements, equipment capabilities, availability, and cost, you can make an informed decision that will help you achieve effective and efficient soil stabilization.
Equipment selection factors
When choosing stabilization equipment, there are several important factors to consider. These factors will help ensure that the equipment you select is appropriate for your specific needs and will effectively stabilize the desired area.
1. Load capacity: One of the most important factors to consider is the load capacity of the equipment. This refers to the maximum weight that the equipment can safely support. It is crucial to choose equipment that can handle the expected load to prevent any accidents or failures.
2. Size and dimensions: The size and dimensions of the equipment are also critical factors to consider. The equipment should fit the available space and be able to maneuver in the desired area. Additionally, it should be compact enough for easy transportation and storage.
3. Stability: The stability of the equipment is another crucial factor. It should have a solid and stable base to ensure that it can effectively stabilize the area. Consider the terrain and environmental conditions where the equipment will be used to determine the level of stability required.
4. Adjustability: The equipment should have adjustable features to accommodate different stabilization needs. This includes adjustable legs, height, angles, and other relevant features. The ability to make precise adjustments will help achieve optimal stabilization results.
5. Durability and reliability: The equipment should be made from high-quality materials that can withstand the demands of stabilization tasks. It should be durable and reliable, able to withstand heavy use and harsh conditions. Look for equipment that comes with warranties or guarantees to ensure its longevity.
6. Safety features: Safety should always be a top priority when selecting stabilization equipment. Look for equipment that has safety features such as non-slip surfaces, safety locks, and emergency stop buttons. These features will help prevent accidents and protect the user.
7. Ease of use: Finally, consider the ease of use of the equipment. It should be user-friendly and intuitive, allowing for easy setup, operation, and maintenance. Complex equipment may require additional training or specialized knowledge, which can add to the overall costs.
By considering these equipment selection factors, you can choose the right stabilization equipment for your specific needs. This will help ensure that your stabilization projects are successful and efficient.
Stages of selecting equipment for a specific facility
When it comes to selecting the right stabilization equipment for a specific facility, there are several important stages that need to be followed. These stages help ensure that the equipment chosen is suitable for the facility’s needs and requirements. Below are the key stages of equipment selection:
Stage | Description |
---|---|
1 | Assessing facility requirements |
2 | Identifying potential equipment options |
3 | Evaluating equipment specifications |
4 | Comparing equipment features and capabilities |
5 | Considering budget and cost-effectiveness |
6 | Consulting with experts and professionals |
7 | Testing and piloting equipment |
8 | Making the final selection |
Each of these stages plays a crucial role in ensuring that the stabilization equipment chosen is the right fit for the specific facility. By following these stages, facility managers can make well-informed decisions and select equipment that will effectively stabilize and support their operations.
Recommendations for choosing the optimal equipment combination
When selecting stabilization equipment for a particular task, it is important to consider several factors to ensure the optimal combination. The following recommendations can help guide your decision-making process:
- Assess the specific stabilization needs: Start by evaluating the specific requirements of the task at hand. Consider factors such as the size and weight of the object that needs to be stabilized, the environment in which the stabilization will take place, and any unique challenges or constraints that need to be addressed.
- Research available equipment: Take the time to research and familiarize yourself with the different types of stabilization equipment available on the market. This may include items such as tripod supports, jacks, wedges, clamps, or braces. Understand the features and capabilities of each type of equipment and how they may align with your specific needs.
- Consider compatibility: Ensure that the equipment you select is compatible with the object or structure that needs to be stabilized. This includes considering factors such as weight capacity, size adjustments, and attachment options. Compatibility is crucial to ensure the equipment can effectively stabilize the object.
- Seek expert advice: If you are unsure about which equipment combination is best suited for your needs, consider consulting with experts in the field of stabilization. They can provide valuable insights and recommendations based on their experience and knowledge.
- Test and evaluate: Before committing to a specific equipment combination, it is advisable to test and evaluate the equipment in realistic conditions. This will help you determine if the chosen combination meets your stabilization requirements effectively. It is also an opportunity to identify any potential issues or limitations.
- Consider budget and long-term use: Finally, take into consideration your budget and long-term use of the equipment. While it may be tempting to opt for the cheapest option, it is important to invest in high-quality equipment that will last and provide reliable stabilization. Consider the value for money, durability, and warranty options when making your decision.
By following these recommendations, you can ensure that you choose the optimal equipment combination for your stabilization needs. Remember to prioritize safety and effectiveness in order to achieve the desired results.
Q&A:
What is stabilization equipment used for?
Stabilization equipment is used to reduce or eliminate unwanted movement or vibrations in various applications. It is commonly used in photography and videography to prevent shaky footage, in construction to stabilize structures, and in the medical field to stabilize patients during surgeries.
How does stabilization equipment work?
Stabilization equipment works by using various mechanisms to counteract unwanted movement or vibrations. In photography and videography, it can use gyroscopes or electronic sensors to detect motion and adjust the camera’s position accordingly. In construction, it can use hydraulic systems or braces to provide stability to structures. In the medical field, it can use specialized beds or restraints to keep patients stable during surgeries.
What are the different types of stabilization equipment?
There are several different types of stabilization equipment available. In photography and videography, there are handheld gimbals, camera stabilizers, and tripods with stabilizing features. In construction, there are jacks, braces, and hydraulic systems. In the medical field, there are specialized surgical tables, patient restraints, and stabilization devices for specific procedures.
Can stabilization equipment be used in sports?
Yes, stabilization equipment can be used in sports to improve performance and prevent injuries. For example, athletes can use stabilizing braces or wraps to support joints and prevent sprains or strains. In golf, there are stabilizing gloves or grips that help improve swing stability. In archery, stabilizers are commonly used to reduce bow vibration and improve accuracy.
Is stabilization equipment expensive?
The cost of stabilization equipment can vary depending on the type and quality of the equipment. Basic handheld gimbals for cameras or smartphones can be relatively affordable, starting at around $100. However, more advanced stabilization systems, such as professional camera stabilizers or medical surgical tables, can be quite expensive, ranging from several hundred to several thousand dollars.
What is stabilization equipment used for?
Stabilization equipment is used to keep things steady and prevent movement or shaking. It is commonly used in photography and videography to reduce camera shake and ensure smooth footage.
What are the different types of stabilization equipment?
There are several types of stabilization equipment, including tripods, gimbals, stabilizer rigs, and image stabilization technology built into cameras or lenses.
How does a tripod help with stabilization?
A tripod is a three-legged stand that provides a stable base for cameras or other equipment. By using a tripod, photographers or videographers can eliminate hand-held camera shake and achieve sharper images or videos.
What is a gimbal and how does it work?
A gimbal is a handheld device or mount that uses motors and sensors to stabilize a camera or other equipment. It allows for smooth movement and eliminates shakes or vibrations, providing steady footage even when the operator is in motion.
Can stabilization equipment be used for other purposes besides photography or videography?
Yes, stabilization equipment can be used in various industries and applications. For example, it is used in aerospace to stabilize satellites or spacecraft, in medical settings to stabilize surgical tools or equipment, and in industrial settings to stabilize machinery or heavy equipment.