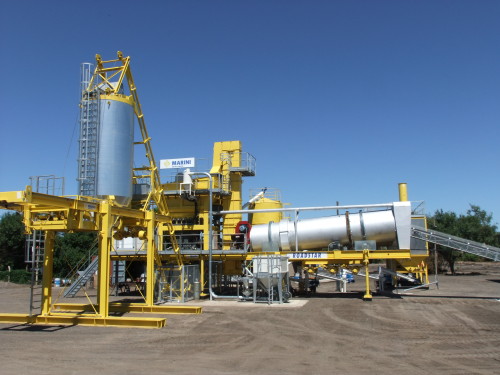
What are the Different Types of Hot Mix Asphalt Plants?
Hot mix asphalt (HMA) is a popular material often used for road construction and maintenance. It is made by heating asphalt cement and mixing it with aggregate, such as sand, gravel, or crushed stone. The result is a strong and durable material that can withstand heavy traffic and harsh weather conditions. However, not all hot mix asphalt is created equal. There are different types of plants that produce HMA, each with its own advantages and limitations.
One type of hot mix asphalt plant is the batch plant. This type of plant produces HMA in batches, meaning that a specific amount is produced at a time. Batch plants are often used for small projects or when different mix designs are required. They are versatile and flexible, allowing for adjustments in temperature and mixing time. However, batch plants can be time-consuming and labor-intensive since each batch must be individually weighed and mixed.
Another type of hot mix asphalt plant is the drum plant. As the name suggests, this type of plant has a drum-shaped mixing chamber where the asphalt is heated and mixed with aggregate. Drum plants are known for their high production capacity and continuous operation. They are often used for large-scale projects or when a consistent mix design is required. However, drum plants can be less flexible than batch plants since adjustments in temperature and mix design may take longer.
In addition to batch and drum plants, there are also continuous mix plants. These plants produce HMA continuously, without the need for batching or drum mixing. They are often used for remote or temporary construction sites, where transportation of materials is challenging. Continuous mix plants are efficient and cost-effective, as they eliminate the need for labor-intensive batching or drum mixing. However, they may not be suitable for projects that require different mix designs or frequent adjustments in temperature.
In conclusion, there are different types of hot mix asphalt plants that can be used to produce HMA. Whether it’s a batch plant, drum plant, or continuous mix plant, each type has its own advantages and limitations. The choice of plant depends on various factors, such as the size and nature of the project, the required mix design, and the available resources. By understanding the different types of plants and their capabilities, construction professionals can make informed decisions and ensure the successful completion of asphalt projects.
Types of Hot Mix Asphalt Plants:
There are different types of hot mix asphalt plants that are used to produce hot mix asphalt (HMA). Each type of plant has its own advantages and is suitable for different types of projects. The various types of hot mix asphalt plants include:
- Batch plants: These plants produce HMA in individual batches. The asphalt is heated and mixed in batch quantities, which allows for better control over the mixture. Batch plants are ideal for small to medium-sized projects.
- Drum plants: These plants produce HMA in a continuous process. The aggregates are heated and mixed in a drum, which allows for a more continuous flow of asphalt production. Drum plants are often used for larger projects.
- Counterflow plants: These plants are similar to drum plants, but the flow of materials is reversed. The aggregates move counter to the flow of the gases. This design allows for better mixing and heating of the materials.
- Parallel flow plants: These plants are similar to drum plants, but the flow of materials is parallel to the flow of the gases. This design allows for more efficient heating and mixing of the materials, resulting in better quality HMA.
- Portable plants: These plants are designed to be easily transported to different job sites. They are compact and can be set up quickly. Portable plants are ideal for remote or temporary projects.
Each type of hot mix asphalt plant has its own advantages and disadvantages. The choice of plant depends on factors such as the size of the project, the required production capacity, and the availability of resources. It is important to carefully consider these factors when selecting a hot mix asphalt plant for a specific project.
Foamed Asphalt Plant
A foamed asphalt plant is one of the different types of hot mix asphalt plants available. It is a unique plant that utilizes foaming technology to produce asphalt mixes.
In a foamed asphalt plant, the hot mix asphalt is produced by injecting a small amount of water into the hot bitumen. This water then vaporizes and expands, creating a foaming effect. The foamed asphalt is then mixed with aggregates to produce the final asphalt mix. This process allows for better coating of aggregates and improved workability of the asphalt mix.
The use of foamed asphalt in hot mix asphalt plants offers several advantages. Firstly, it allows for the use of higher percentages of reclaimed asphalt pavement (RAP) in the mix. The foamed asphalt can effectively bind the aged RAP, improving the overall performance of the mix.
Additionally, foamed asphalt mixes tend to have better rutting resistance and improved durability compared to traditional hot mix asphalt. The foaming process also helps to reduce the production temperature of the asphalt mix, resulting in energy savings and reduced emissions.
Overall, foamed asphalt plants are a valuable addition to the different types of hot mix asphalt plants available. They offer improved performance, sustainability, and cost-effectiveness, making them a popular choice for asphalt producers.
Batch Asphalt Plant
A batch asphalt plant is one of the different types of hot mix asphalt plants. It is called a batch plant because the asphalt mixture is produced in batches.
Batch plants are ideal for small to medium-sized projects and are often used for road construction and maintenance. They are versatile and can be customized to meet specific project requirements.
Here are some key features of batch asphalt plants:
- Accurate and consistent mix: Batch plants produce asphalt mixtures in precise quantities, ensuring consistent quality with each batch.
- Flexibility: Batch plants allow for easy adjustments to the asphalt mix design, making it possible to produce different types of mixtures, including stone matrix asphalt and porous asphalt.
- Efficiency: Batch plants can produce high-quality asphalt mixtures quickly and efficiently. The entire process, from feeding the aggregates to discharging the hot mix, can be completed in a short amount of time.
- Quality control: Batch plants provide better control over the production process, allowing for thorough testing and monitoring. This helps ensure that the asphalt mixture meets the required specifications.
- Environmental friendliness: Batch plants are equipped with pollution control devices, such as baghouses, to capture the dust and emissions generated during the production process. This helps minimize the impact on the environment.
Overall, batch asphalt plants offer a reliable and efficient solution for producing hot mix asphalt. They are widely used in the construction industry and continue to evolve to meet the demands of different projects.
Continuous Asphalt Plant
A continuous asphalt plant is one of the different types of hot mix asphalt plants available. Unlike batch plants, which produce asphalt in discrete batches, a continuous plant produces asphalt continuously without any interruption. This continuous production process offers several advantages:
- High Efficiency: Continuous plants are designed to operate efficiently, producing a steady supply of hot mix asphalt without the need to stop and start between batches.
- More Uniform Mix: Since the production is continuous, the asphalt mix is more uniform throughout the entire production process. This leads to a higher quality end product.
- Less Wasted Materials: Continuous plants eliminate the need for starting and stopping, which reduces the amount of wasted materials during each production cycle.
- Flexible Production: Continuous plants have the ability to adjust the production rate based on the specific requirements of the project. This allows for greater flexibility in meeting varying demand levels.
The continuous asphalt plant typically consists of several components, including:
- Drying Drum: This is where the aggregate is heated and dried before being mixed with the liquid asphalt.
- Mixing Tower: The heated aggregate is mixed with the liquid asphalt in the mixing tower to produce hot mix asphalt.
- Hot Storage Silo: The finished asphalt mix is stored in a hot storage silo until it is ready to be loaded onto trucks for transportation to the construction site.
- Control System: A control system is used to monitor and control the various processes and components of the continuous plant to ensure smooth and efficient operation.
Continuous plants are commonly used for large-scale asphalt production projects where a consistent supply of hot mix asphalt is required. They are often preferred for their high efficiency, flexibility, and ability to produce a uniform mix. However, they may not be suitable for smaller projects or situations where the demand for asphalt fluctuates significantly.
Stationary Asphalt Plant
A stationary asphalt plant is one of the various types of hot mix asphalt plants available. It is designed to manufacture asphalt concrete, which is a mixture of asphalt binder and aggregates, at a fixed location. This type of plant is commonly used for large-scale asphalt production projects.
Here are some key features and advantages of a stationary asphalt plant:
- Continuous operation: Stationary asphalt plants are capable of producing asphalt mix continuously, without any interruption. This ensures a steady supply of hot mix asphalt.
- High production capacity: These plants are known for their high production capacity, making them suitable for large construction projects where a significant amount of asphalt is required.
- Efficient heating and mixing: Stationary asphalt plants are equipped with advanced heating and mixing systems that ensure thorough and efficient mixing of asphalt binder and aggregates, resulting in high-quality asphalt mix.
- Controlled production process: These plants offer precise control over the production process, allowing operators to adjust the parameters and maintain consistency in the asphalt mix produced.
- Easy maintenance: Stationary asphalt plants are designed for easy maintenance, with readily accessible components and parts. This ensures minimal downtime and reduces maintenance costs.
A typical stationary asphalt plant consists of various components, including a cold aggregate feeder, drying drum, hot aggregate elevator, hot mix storage silo, and control panel. The plant operates by feeding the aggregates into the drying drum, where they are heated and dried. The dried aggregates are then mixed with the asphalt binder in the hot mix elevator. The resulting hot mix asphalt is stored in the silo before it is transported to the construction site.
Overall, a stationary asphalt plant is a reliable and efficient option for producing hot mix asphalt in a fixed location. Its high production capacity and precise control over the production process make it suitable for large construction projects. With regular maintenance, a stationary asphalt plant can provide continuous and consistent supply of high-quality asphalt mix.
Mobile Asphalt Plant
A mobile asphalt plant is a type of hot mix asphalt plant that is designed to be easily transported from one location to another. Unlike stationary asphalt plants, which are permanently installed in a specific location, mobile asphalt plants are portable and can be set up and dismantled quickly.
Mobile asphalt plants are commonly used for small to medium-sized projects or for projects that require frequent relocation. They are ideal for road construction projects in remote areas or projects that require the production of asphalt at multiple locations.
There are several advantages to using a mobile asphalt plant:
- Flexibility: Mobile asphalt plants can be easily transported to different locations, allowing for greater flexibility in project planning and execution.
- Cost-Effectiveness: Mobile asphalt plants are generally more cost-effective than stationary plants, as they require less infrastructure and can be operated with fewer personnel.
- Quick Installation: Mobile asphalt plants can be set up and ready for operation in a short period of time, reducing project downtime.
Mobile asphalt plants are available in different capacities and configurations to suit various project requirements. They can produce hot mix asphalt of different grades to meet the specific needs of the project.
Overall, mobile asphalt plants offer a convenient and efficient solution for asphalt production in different locations. Whether it’s a road construction project in a remote area or a project that requires frequent mobility, a mobile asphalt plant is a reliable and cost-effective choice.
Portable Asphalt Plant
A portable asphalt plant is a hot mix asphalt plant that can be easily transported and set up at different locations for on-site production of asphalt. This type of plant is ideal for projects with short construction timelines or for contractors who need to move their operations frequently.
The portable asphalt plant operates in the same way as other hot mix asphalt plants, but with the added advantage of mobility. It consists of different components that work together to produce high-quality asphalt mix:
- Drying and Heating System: The drying and heating system in a portable asphalt plant uses a burner to heat the aggregates and remove any moisture content. This ensures that the aggregates are properly dried before being mixed with the asphalt binder.
- Mixing System: The mixing system combines the dried aggregates with the hot asphalt binder to create the asphalt mix. This system includes a twin-shaft paddle mixer that ensures thorough mixing of the components.
- Storage Silos: The portable asphalt plant features storage silos for storing the hot asphalt mix. These silos have a large capacity and can hold enough mix for the project’s duration.
- Control System: A control system is installed in the portable asphalt plant to monitor and control the operations. It allows the operator to adjust the mix proportions, temperature, and other parameters to ensure consistent and high-quality asphalt production.
One of the main advantages of a portable asphalt plant is its flexibility and versatility. It can be easily transported to different job sites, reducing the need for multiple plants and saving time and money. Additionally, its compact design allows for quick setup and dismantling, enabling contractors to start production promptly.
Portable asphalt plants are suitable for various applications, including road construction, repair, and maintenance projects. They can produce different types of hot mix asphalt, such as dense-graded asphalt, open-graded asphalt, and gap-graded asphalt, to meet specific project requirements.
Overall, a portable asphalt plant offers convenience, efficiency, and cost-effectiveness for contractors who need to produce hot mix asphalt at different locations and on short notice. Its mobility and ease of setup make it a valuable asset in the asphalt industry.
Drum Mix Asphalt Plant
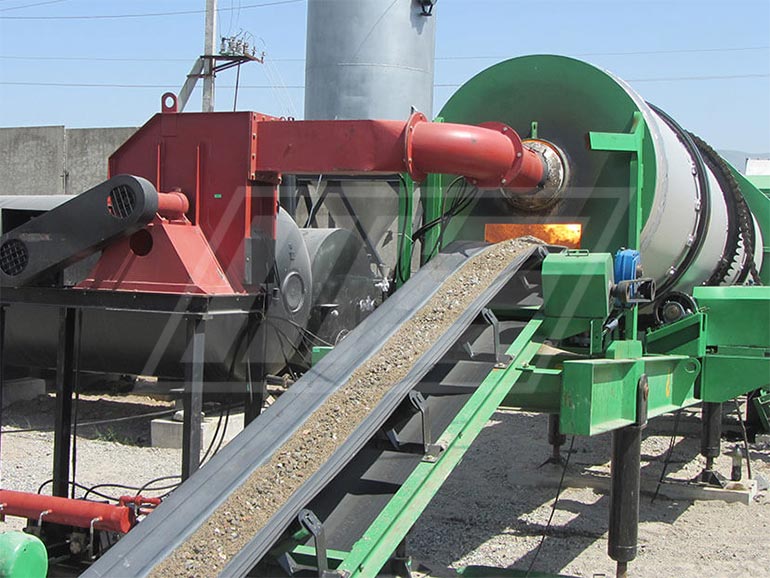
A drum mix asphalt plant is a type of asphalt plant that produces hot mix asphalt (HMA) in a continuous process. It is different from other types of asphalt plants, such as batch plants or parallel flow plants, because it uses a rotating drum to mix the aggregates, asphalt binder, and filler materials.
The drum mix asphalt plant consists of a cold aggregate feeder system, a drying and mixing drum, a burner, a baghouse dust collection system, and a control system. The cold aggregate feeder system is responsible for feeding the different sizes of aggregates into the drying and mixing drum. The drying and mixing drum is where the aggregates are dried, heated, and mixed with the asphalt binder and filler materials to produce HMA.
The burner in a drum mix asphalt plant is used to provide the heat necessary to dry and heat the aggregates. It can be fueled by natural gas, diesel, or other fuels. The baghouse dust collection system is used to capture and filter out the dust and fines generated during the production process. The control system is responsible for controlling and monitoring the various components of the plant.
One of the advantages of a drum mix asphalt plant is its ability to produce HMA continuously, without the need to stop and start the production process. This makes it more efficient and cost-effective compared to other types of asphalt plants. Another advantage is that the drum mix asphalt plant can produce high-quality HMA with consistent gradation and asphalt content.
In summary, a drum mix asphalt plant is a type of asphalt plant that uses a rotating drum to mix the aggregates, asphalt binder, and filler materials to produce hot mix asphalt. It offers advantages such as continuous production and high-quality HMA.
Counterflow Asphalt Plant
The counterflow asphalt plant is one of the different types of hot mix asphalt plants. It is designed to mix and produce asphalt at high temperatures to ensure the desired quality and consistency of the finished product.
What sets the counterflow asphalt plant apart is its unique design that allows for the mixing of the aggregates and the binder (asphalt) to occur in separate chambers.
In a counterflow plant, the aggregates are introduced at the lower end of the drum and move upward as they mix with the hot gases and asphalt binder. The heated aggregates are then transported to the top of the drum by the help of flights, while the remaining gases and dust particles are eliminated through the exhaust system.
This reverse flow of materials and gases allows for better mixing and heat transfer, resulting in a more uniform distribution of the asphalt binder throughout the aggregate mix. It also helps in reducing emissions and improving fuel efficiency.
The counterflow asphalt plant is ideal for producing high-quality hot mix asphalt with reduced emissions. It is commonly used for road construction projects where durability and superior performance are required.
Overall, the counterflow asphalt plant offers several advantages over other types of asphalt plants. These include improved mixing efficiency, reduced emissions, and enhanced fuel economy. Its unique design and operational capabilities make it a popular choice among asphalt producers worldwide.
Parallel Flow Asphalt Plant
A parallel flow asphalt plant is one of the different types of hot mix asphalt plants. It is called “parallel flow” because the aggregate and the hot gases flow in parallel down the drum. This type of plant is commonly used for high production rates and large quantities of asphalt.
Parallel flow asphalt plants have several components:
- Cold Feed System: The cold feed system is responsible for storing and delivering the different sizes of aggregates to the drying drum.
- Drying Drum: The drying drum is where the aggregates are heated and dried. It is equipped with flights inside to promote thorough mixing and drying.
- Burner: The burner is responsible for heating the aggregates and maintaining the temperature inside the drying drum.
- Hot Mix Storage Silo: The hot mix storage silo is used to store the final product before it is loaded onto trucks for transportation to the construction site.
- Baghouse System: The baghouse system is responsible for filtering the hot gases produced during the drying process, removing any dust or pollutants before they are released into the atmosphere.
Parallel flow asphalt plants offer several advantages. They have a higher production capacity compared to other types of plants, making them suitable for large-scale projects. Additionally, the parallel flow design allows for better control over the mixing process, resulting in a high-quality asphalt mix.
However, parallel flow asphalt plants also have some limitations. They require more space due to their large size and can be more expensive to operate and maintain compared to other types of plants. Additionally, they may produce higher emissions compared to counterflow plants, although the use of a baghouse system helps to minimize environmental impact.
Overall, the parallel flow asphalt plant is a popular choice for hot mix asphalt production due to its high production capacity and the ability to produce high-quality asphalt mixes.
Double Barrel Asphalt Plant
A Double Barrel Asphalt Plant is one of the many types of hot mix asphalt plants available. The term “double barrel” refers to the unique design of this particular plant, which allows for the simultaneous production of two different types of asphalt mix. This feature sets it apart from other plants that typically produce only one type of mix at a time.
The Double Barrel Asphalt Plant consists of two separate drum mixers, each of which can produce its own type of asphalt mix. These drum mixers operate in parallel, allowing for a continuous production process and increased efficiency. By having two drum mixers, asphalt producers have the flexibility to produce different types of mix, such as hot mix asphalt (HMA) and warm mix asphalt (WMA), simultaneously.
The main advantage of the Double Barrel Asphalt Plant is its versatility. With the ability to produce two different types of asphalt mix at the same time, it provides asphalt producers with greater flexibility in meeting the varying demands of their customers. For example, an asphalt producer can easily switch between producing HMA and WMA depending on the specific project requirements or customer preferences.
In addition to its versatility, the Double Barrel Asphalt Plant also offers other benefits. The parallel operation of the drum mixers allows for faster production rates compared to plants with a single drum mixer. The continuous production process ensures a constant supply of hot mix asphalt, minimizing downtime and maximizing productivity.
The Double Barrel Asphalt Plant typically features advanced technologies and controls to optimize performance. This includes automated controls for accurate temperature and moisture control, as well as systems for monitoring and adjusting the asphalt mix proportions. These features ensure consistent quality and performance of the asphalt mix produced by the plant.
In conclusion, the Double Barrel Asphalt Plant is a unique type of hot mix asphalt plant that allows for the simultaneous production of two different types of asphalt mix. Its versatility, efficiency, and advanced technologies make it a preferred choice for asphalt producers looking to meet the diverse demands of their customers while maintaining high-quality standards.
Novel Technologies in Asphalt Plant Design
The hot mix asphalt plants industry is continuously evolving, and new technologies are being introduced to enhance efficiency, productivity, and sustainability in asphalt production. Here are some of the novel technologies in asphalt plant design:
- Recycled Asphalt Pavement (RAP) Systems: Many modern asphalt plants are equipped with RAP systems, which allow for the recycling of old asphalt pavement. RAP systems crush and screen the old asphalt, removing any contaminants, and then reintroduce it into the mix. This not only reduces the need for virgin aggregate but also improves the sustainability of the plant by reducing waste.
- Warm Mix Asphalt (WMA) Technology: WMA technology allows for the production of asphalt at lower temperatures compared to traditional hot mix asphalt plants. This technology uses additives or foaming techniques to reduce the viscosity of the asphalt, making it easier to work with at lower temperatures. WMA technology offers several benefits, including reduced energy consumption, lower emissions, and improved workability.
- Continuous Mixing Plants: Continuous mixing plants, also known as drum mix plants, offer a continuous production process. In these plants, the aggregates are continuously fed into the drum, where they are heated and mixed with the asphalt binder. Continuous mixing plants are known for their high production rates and are ideal for large-scale projects.
- Multicyclone Systems: Multicyclone systems are used to control air pollution in asphalt plants by removing particulate matter from the exhaust gases. These systems use a series of cyclones to separate the particles from the gas stream. Multicyclone systems are more efficient and have a smaller footprint compared to traditional baghouse filters.
- Automatic Plant Control Systems: Today’s asphalt plants often feature advanced control systems that automate various aspects of the production process. These systems monitor and control variables such as aggregate feed rates, temperature, and asphalt binder content, ensuring consistent mix quality and reducing human error. Automatic plant control systems improve efficiency, reduce costs, and enhance overall plant performance.
These novel technologies are revolutionizing the asphalt industry, making asphalt production more sustainable, cost-effective, and environmentally friendly. As the demand for high-quality asphalt continues to grow, the development of new technologies will play a crucial role in meeting this demand and shaping the future of asphalt plant design.
Environmental Considerations for Asphalt Plants
Asphalt plants play a crucial role in the construction industry, their primary function being the production of hot mix asphalt, which is used in various paving applications. However, it is essential to consider the environmental impact of these plants and implement measures to minimize their adverse effects.
There are different types of hot mix asphalt plants, each with its own environmental considerations. Some of the key environmental considerations include:
- Emissions: Hot mix asphalt plants can emit various pollutants, including particulate matter (PM), sulfur dioxide (SO₂), nitrogen oxides (NOₓ), carbon monoxide (CO), and volatile organic compounds (VOCs). To mitigate these emissions, plants employ various techniques, such as baghouses, wet scrubbers, and stack filters, to capture and reduce pollutants.
- Noise: Asphalt plant operations can be noisy due to the use of heavy machinery and equipment. Plant operators should implement noise control measures, such as sound barriers and equipment enclosures, to minimize the impact on nearby communities.
- Water usage: Asphalt production requires water for processes like cooling and dust suppression. However, excessive water usage can lead to environmental concerns, such as the depletion of local water sources. Plants should optimize water usage and consider recycling and reusing water whenever possible.
- Waste management: Asphalt plants generate waste materials, such as asphalt millings and excess asphalt mix. These waste materials should be properly managed and disposed of according to local regulations. Recycling and reusing waste materials can also be a sustainable option.
- Energy consumption: Asphalt plants consume significant amounts of energy for heating aggregates and producing hot mix asphalt. Implementing energy-efficient technologies and practices, such as using recycled asphalt pavement (RAP) and optimizing plant operations, can help reduce energy consumption and associated greenhouse gas emissions.
Overall, environmental considerations for asphalt plants are crucial to minimize their impact on air quality, water resources, and surrounding communities. By adopting sustainable practices and technologies, the industry can continue to provide essential asphalt products while reducing its environmental footprint.
Advantages of Using Hot Mix Asphalt Plants
Hot mix asphalt plants offer several advantages over other types of asphalt plants. Here are some of the key benefits:
- High-quality asphalt: Hot mix asphalt plants produce high-quality asphalt that is suitable for various applications. The hot mixing process ensures that the asphalt is well-mixed and evenly coated with aggregates, resulting in a smooth and durable surface.
- Cost-effective: Hot mix asphalt plants are cost-effective in the long run. While the initial investment may be higher compared to other types of plants, the high-quality asphalt produced by these plants requires less maintenance and repair, reducing overall expenses in the future.
- Flexible production: Hot mix asphalt plants can produce different types of asphalt mixes to meet specific project requirements. They can produce hot mix asphalt, warm mix asphalt, and cold mix asphalt, allowing for greater flexibility in construction projects.
- Fast and efficient: Hot mix asphalt plants are designed for fast and efficient production. The hot mixing process allows for quick heating and mixing of asphalt, resulting in faster production times and increased productivity.
- Environmental friendly: Hot mix asphalt plants are designed to be environmentally friendly. They incorporate various technologies to reduce emissions and control pollution, ensuring compliance with environmental regulations.
- Consistency and reliability: Hot mix asphalt plants provide consistent and reliable asphalt mixes. The controlled mixing process ensures that each batch of asphalt meets the required specifications, resulting in consistent performance and quality.
- Easy to operate: Hot mix asphalt plants are relatively easy to operate. Most modern plants are equipped with user-friendly interfaces and automated control systems, making it easier for operators to monitor and control the production process.
Q&A:
What are the main types of hot mix asphalt plants?
The main types of hot mix asphalt plants include batch mix plants, drum mix plants, and continuous mix plants.
What is a batch mix plant?
A batch mix plant is a type of hot mix plant where the asphalt is produced in batches. In this type of plant, the aggregates are mixed with the asphalt binder in specific proportions to produce a high-quality asphalt mixture.
What is a drum mix plant?
A drum mix plant is a type of hot mix plant where the asphalt is produced in a continuous process. The aggregates are heated and mixed with the asphalt binder in a rotating drum, resulting in a uniform mixture.
What is a continuous mix plant?
A continuous mix plant is a type of hot mix plant where the asphalt is produced in a continuous process. In this type of plant, the aggregates and the asphalt binder are continuously fed into a mixing drum, resulting in a continuous production of hot mix asphalt.
What are the advantages of using a continuous mix plant?
The advantages of using a continuous mix plant include a higher production capacity, a more efficient and continuous operation, and the ability to produce a wide range of asphalt mixtures with different aggregate proportions.